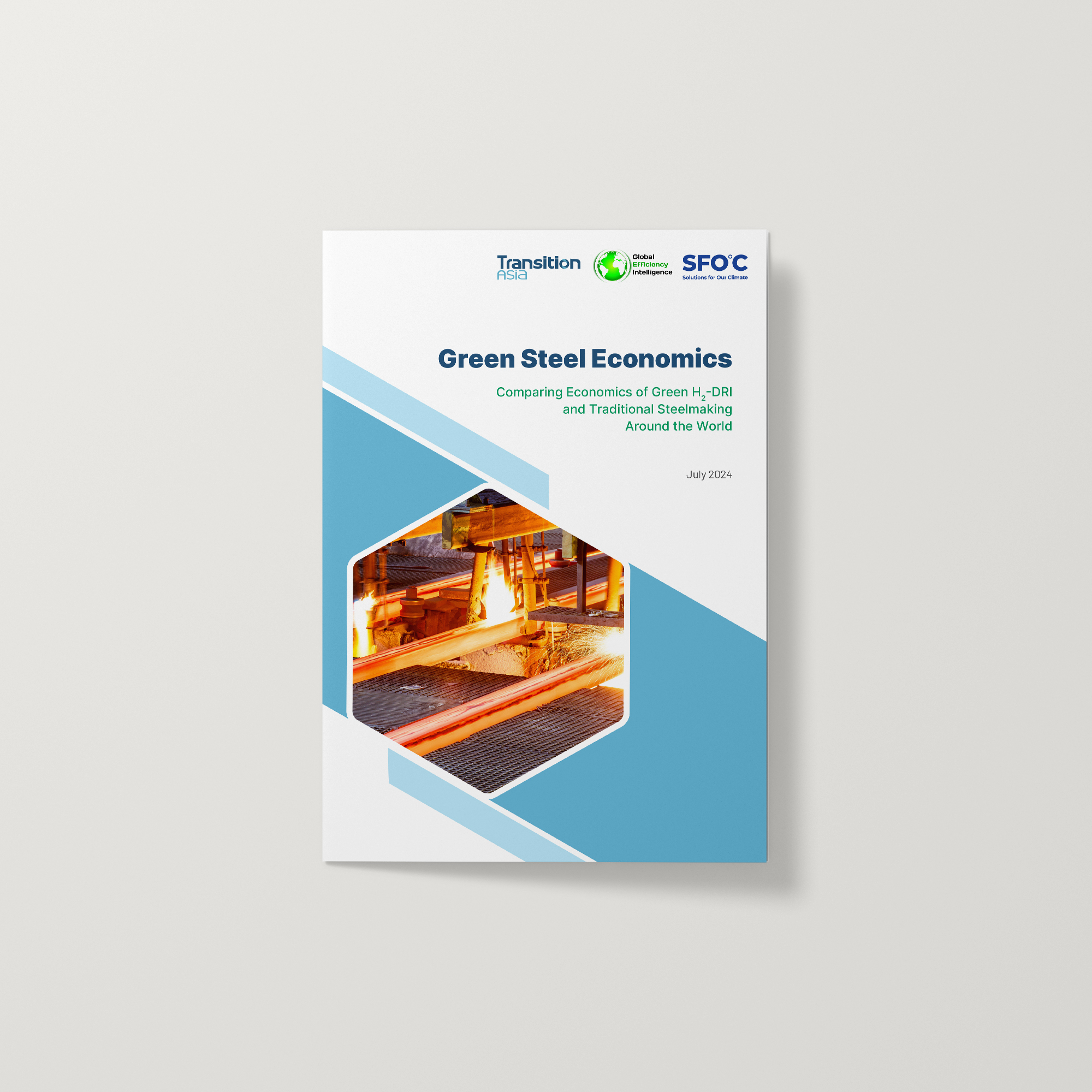
Executive summary
The global steel industry accounted for over 7% of global greenhouse gas (GHG) emissions and over 11% of global CO2 emissions. The Hydrogen Direct Reduced Iron (H2-DRI) process utilizing green hydrogen from renewable sources promises significant emission reductions and a transition to greener steel production in the sector. The adoption of green H2-DRI-EAF steelmaking involves financial considerations varying by country, influenced by hydrogen costs and carbon pricing mechanisms investigated in this study.
This study by Global Efficiency Intelligence, Transition Asia, and Solutions for Our Climate assesses the costs of green H2-DRI-EAF steelmaking compared to traditional Blast Furnace-Basic Oxygen Furnace (BF-BOF) and Natural Gas Direct Reduced Iron-Electric Arc Furnace (NG-DRI-EAF) routes across seven major steel-producing countries, including the U.S., EU, China, Japan, South Korea, Brazil, and Australia. It utilizes a detailed financial model to calculate the levelized cost of steel (LCOS) ($/ton of steel) using expenses such as capital investments, raw materials, labor, and energy costs, adjusting for varying levels of hydrogen use. Different levels of H2 and carbon prices are included in this analysis.
As green-steel incurs a cost premium, this directly affects the material costs of downstream use sectors. This study has analyzed the potential cost increases related to three notable downstream sectors; automobile ($/car), construction ($/building unit) and shipping ($/ship), using steel produced via the H2-DRI-EAF method compared to conventional methods for those sectors.
Our study includes critical components such as the gradual substitution of natural gas with green hydrogen (H2) in the DRI route, the integration of renewable energy and green H2 production, and the required of electrolyzer capacity. Additionally, we discuss international experiences with financing H2-DRI projects.